TPM設備全面健康管理模式的構建與實踐
來源/作者: TPM咨詢服務中心 丨 發(fā)布時間:2017-12-07 丨 瀏覽次數(shù):
一、全面健康管理模式構建背景
日照港集團嵐山港務有限公司機械二公司成立于2012年11月,主要承擔港口貨物裝卸和進口大型裝載機、輪胎吊、叉車和龍門吊等大型機械的使用管理工作。
?。ㄒ唬﹤鹘y(tǒng)設備管理階段
傳統(tǒng)設備管理以設備故障維修為核心,以被動保養(yǎng)、排故診斷、解體換件修理為基本模式,重點關注設備的故障階段因其局限性,導致存在如下問題:一是操作人員重使用、輕保養(yǎng);二是維修人員成本意識不足;三是設備利用率高、故障頻次高、維修費用高。
(二)設備管理源頭回溯階段
2012-2013年,我們以設備故障管理為切入點,通過查找故障在技術、人為、管理層面發(fā)生的源頭,分析制定根除措施,持續(xù)改進,杜絕故障擴大或重復發(fā)生,逐漸摸索形成了一套設備管理源頭回溯機制。但依然無法做到對設備劣化狀態(tài)和突發(fā)故障完全有效的掌控,設備突發(fā)故障仍時有發(fā)生。我們意識到,對設備日常的規(guī)范管理和對微小缺陷的及早處置,能夠有效抑制其向中缺陷的演變,減緩故障的發(fā)生。2014年以來,我們?yōu)閷で笠环N更好的管理方法一直在努力思索。
?。ㄈ┰O備全面健康管理探索階段
1、中西醫(yī)健康養(yǎng)生理論
《黃帝內經》講上醫(yī)治未病,強調預防,強調健康促進,養(yǎng)生、保健治療較治愈疾病更加重要。
世界衛(wèi)生組織指出,醫(yī)學發(fā)展戰(zhàn)略優(yōu)先從以治愈疾病為目的的高技術追求轉向預防疾病與損傷,維持和促進健康。只有以預防疾病、促進健康為首要目的的醫(yī)學才是可持續(xù)的。醫(yī)學發(fā)展正由治愈疾病向預防疾病轉變,由疾病醫(yī)學向健康醫(yī)學轉變,由強調醫(yī)生的作用轉向更加重視病人的自我保健。
受到中醫(yī)養(yǎng)生保健精髓和西醫(yī)健康醫(yī)學理論啟發(fā),拓展到設備管理中,一是鎖定設備故障苗頭后要及早解決,一旦延誤則故障擴大,維修成本增加甚至無法修復,導致報廢;二是從故障誘因、故障苗頭到發(fā)生故障,設備在不同的階段采取不同檢維修策略。
2、設備健康管理理論
傳統(tǒng)的設備管理從事后維修(故障維修),進步到預防維修,但考慮到盲目的預防可能造成維修不足或維修過剩,又產生預知-狀態(tài)維修概念。狀態(tài)維修是在設備劣化P-F間隔期的維修,這時設備已進入劣化狀態(tài),如果不進行維修就可能發(fā)生故障。
間隔
傳統(tǒng)維修管理一般會認為,過早對設備的維修-維護活動是不經濟的,甚至會導致設備的損壞。我們換一個角度思考,如果設備早期的維護活動設計合理,是否可能做到無損害,同時是最經濟的狀況?答案是肯定的。這樣,我們將設備狀態(tài)管理延伸到設備早期,類似于人類,稱之為健康管理。設備健康管理突破設備無故障就是完好的二值邏輯思維,將健康狀況看成是[0,1]區(qū)間連續(xù)值,也就是說,設備狀況是由健康向亞健康、向故障逐漸演變的。
二、工作思路
設備全面健康管理模式工作思路是重點鎖定設備健康和亞健康階段,追求設備全壽命周期健康,以自主維修、預防管理、自主維護三點為支撐,致力于人員綜合素養(yǎng)的提高和設備綜合效能的提升。
設備全面健康管理模型
我們將管理體系中部門、崗位職責和績效重新定位,對原有的的設備管理理念、策略、方法進行了全面深入的優(yōu)化,將設備擬人化:設備好比作人,操作司機對應著監(jiān)護人,設備所在隊則相當于家庭,設備所在隊內設置的技術組好比家庭醫(yī)生。維修備件倉庫好比藥房,維修人員如同專業(yè)醫(yī)生,維修隊就是醫(yī)院。負責設備技術管理的技術室,則相當于健康管理部門。
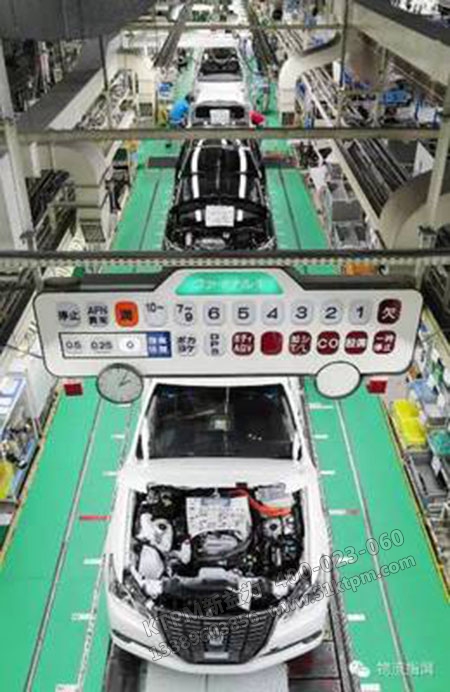
全面健康管理
各崗位、部門職責定位優(yōu)化
三、TPM管理培訓公司的工作措施
(一)開展自主維修,快速治愈設備故障
1、設備所在隊充分發(fā)揮設備主體作用,在發(fā)現(xiàn)設備異常后主動調度資源進行修復。首先是調整、緊固、除銹等力所能及的項目由司機自行維護;其次是司機無法修復的由承擔家庭醫(yī)生角色的技術組成員進行維修;再次是由維修隊實施專業(yè)維修。
2、按照PDCA閉環(huán)管理原則,強化維修組織,完善維修計劃、規(guī)范維修實施,注重總結與經驗積累,通過制定維修標準,規(guī)范維修行為,提高維修質量和效率。
強化維修組織,持續(xù)改善,日臻規(guī)范
3、建立故障防范管理閉環(huán),明確故障分類和處理過程,運用三高一長統(tǒng)計結果,進行趨勢分析、TOP項回溯與跟蹤解決。
定期分析設備故障情況,查找重點項予以解決
4、堅持問題導向,創(chuàng)新并優(yōu)化設備管理源頭回溯機制,查找問題根源,杜絕故障擴大或同類問題再次發(fā)生。
如針對滲漏油問題,從人-機-料-法-環(huán)查找要因,并采取針對性措施予以解決。一是規(guī)范操作,杜絕超載等違規(guī)作業(yè);二是查找改進設備設計缺陷,改進密封工藝;三是提升液壓管件質量;四是建立滲漏油檢修標準,提高維修質量。
5、強化技術攻關,掌握了進口設備發(fā)動機、變速箱核心技術,以及臂架系統(tǒng)修復再造、鏟斗大修等工藝,實現(xiàn)了進口設備自主維修。在設備自主維修及技術攻關過程中,注重設備故障診斷小組作用發(fā)揮,提升了疑難故障快速診斷、排除能力,提高維修效率,并為拓展自主維修打造人才梯隊。
6、加強維修備件管理,建設標準化、系統(tǒng)化、便捷化的備件倉庫,梳理完善物資周期定額,規(guī)范舊件循環(huán)使用,完善激勵措施并形成長效機制。
持續(xù)改善的定額管理機制
?。ǘ┝ν祁A防管理,消除設備亞健康
據(jù)統(tǒng)計,目前在用的機械設備,健康狀態(tài)的約占20%,亞健康狀態(tài)的約占60%,故障狀態(tài)的約占20%。亞健康是設備形態(tài)和性能的亞穩(wěn)態(tài),具備雙向轉化的特性,及時診斷處理,可以轉化為健康;診斷處理不當,可劣化為故障。我們將管理重心向亞健康狀態(tài)的設備調整,由此牢牢掌握了設備健康管理的主動權。
1、成立設備隊技術組,堅持管理重心下移,實施設備精準點檢,及時發(fā)現(xiàn)設備故障苗頭,準確識別、重點管控亞健康狀態(tài),快速恢復健康狀態(tài)。
充分發(fā)揮技術組作用g
2、建立油品檢測分析機制,如同醫(yī)院抽血化驗,綜合分析部件磨損情況,掌握設備劣化趨勢,維修診斷更加準確,避免了過維修或欠維修。
有效運用油品檢測分析結果輔助維修
油品檢測分析機制的運行促進了按質換油的實現(xiàn),通過對設備使用油品進行連續(xù)檢測,在油質不發(fā)生變化的情況下適當延長更換時間。另外,還使我們不再依賴廠家指定油品,而是選擇同品質、價位更低或是更高品質、性價比更高的油品。以機油為例,年可節(jié)約50萬元。
3、定期讀取車載電腦中設備運行數(shù)據(jù),了解設備運行狀況,糾正操作司機誤操作、惡意操作、習慣違章等行為,最大程度的保障設備安全運行,降低油耗。
讀取設備運行數(shù)據(jù),及時糾正發(fā)現(xiàn)問題
4、建立發(fā)動機油消耗分析機制,根據(jù)機油消耗變化量,掌控發(fā)動機活塞環(huán)劣化狀態(tài),實現(xiàn)了發(fā)動機3萬臺時活塞、缸套無更換,現(xiàn)在向4萬臺時努力。近年來,除1臺裝載機發(fā)動機進行過活塞、缸套更換外,其他發(fā)動機均控制到只更換活塞環(huán),依然達到原有技術性能要求,保持了發(fā)動機良好的工作狀態(tài)。
5、開展?jié)B漏油專項治理,以液壓部件無滲漏為目標,預防液壓系統(tǒng)故障。
一是在原有自主壓制管件基礎上升級壓管設備,實現(xiàn)全部油管自主壓制,應用脈沖試驗臺檢驗管件質量和掌控管件在每個階段的承壓情況,實現(xiàn)了管件全壽命周期的管理。
實現(xiàn)液壓管件全壽命周期管理
二是探索應用異形密封,改進液壓部件密封質量,以達到更好的密封效果。
探索應用異形密封
6、強化設備防自燃控制,建立圖文并茂、操作性強的《設備防自燃關鍵點及控制措施表》,強化落實,確保了設備消防安全。
7、實施預防性檢修,及時消除故障苗頭。
一是自主建立驅動橋拆檢標準,在設備運行到2-2.4萬臺時間實施預防檢修,通過更換軸承等易損件,調整工作間隙等措施,避免了連鎖故障。
二是及早發(fā)現(xiàn)設備設計缺陷,對VOLVOL220F系列裝載機變速箱二檔過油管路進行技術改造,解決了廠家未能解決的問題。
三是對大連叉車三菱HD24-1型變速箱檔位行星齒輪軸定位銷軸改造,避免了因銷軸脫落而造成的變速箱部件損壞。
?。ㄈ娀灾骶S護,確保設備健康養(yǎng)生
養(yǎng)生可以使健康持久,設備也同樣如此。
1、規(guī)范使用,從源頭消除設備故障誘因;規(guī)范檢查,及時發(fā)現(xiàn)設備異常;規(guī)范保養(yǎng),使設備處于健康養(yǎng)護狀態(tài)。通過完善設備作業(yè)標準,制定設備點檢、潤滑、清掃基準書,形成設備養(yǎng)生手冊,使日常工作有標準、有指導;落實班組、室隊、公司三級監(jiān)督,確保自主維護執(zhí)行到位。
2、采用單點課、視頻、現(xiàn)場講解等形式培訓,提升操作人員能力,利用班前一問、應知應會知識考試、現(xiàn)場抽查等驗證培訓效果。
圖文并茂的標準為流程化作業(yè)提供了指導,完備的監(jiān)督機制強化了工作的執(zhí)行與落實,豐富多樣化的培訓使司機快速、全面的加深對設備的認識,使司機自覺形成養(yǎng)護設備、愛護設備的良好習慣。
?。ㄋ模┩菩锌冃C制,實現(xiàn)人機精細管理
設備健康、亞健康、故障三個階段的良好狀態(tài)是以人為載體實現(xiàn)的,通過人員、經濟、技術管理相結合,建立全面健康績效管理機制,設置KPI,采取過程控制方法實現(xiàn)管理目標。
1、操作人員用好、養(yǎng)好設備
實施定人定車、單車核算,將燃油費用、維修費按照一定比例攤分到個人,利用工資杠桿調控,調動操作司機主觀能動性。
開展自主維護工具開發(fā)大賽,提高員工自主維護的積極性,員工自發(fā)設計一批實用性較強的工具,使檢查、保養(yǎng)質量得以保證。
2、維修人員修好設備
采用工時定額管理維修人員績效,使維修人員主動排除故障,提高維修效率。
3、技術人員管好設備
實施技術管理人員劃片承包責任制,片內設備管理成效與工資掛鉤,提高技術人員能動性和積極性。
開展員工技能和五星級車輛評定活動,逐級晉升,調動員工積極性。
四、取得成效
?。ㄒ唬┰O備管理指標向好
完好率保持98.4%以上,故障率2.9%以下。
(二)科技創(chuàng)新能力提高
獲得國家實用新型專利48項;設備管理源頭回溯機制獲得中國設備管理協(xié)會設備管理創(chuàng)新成果二等獎,山東省設備管理協(xié)會設備管理成果一等獎;大型進口裝載機工作系統(tǒng)修復再造獲得山東省設備管理成果二等獎。
?。ㄈ┕芾沓杀窘档?/div>
公司單位考核成本呈逐年下降的趨勢,從2012年底的0.47元/噸,實現(xiàn)了三連降,2014年0.31元/噸,2015年單位考核成本0.24元/噸。若以8000萬噸/年的操作量計算,僅2014-2015年節(jié)約成本1280萬元。
五、持續(xù)改善
2016年,我們將在設備全面健康管理模式構建的基礎上,持續(xù)完善體系,與卓越績效、全面規(guī)范化的生產維護(TnPM)深度融合,強化信息化技術運用,加強技術交流、借鑒先進理念、先進技術和先進經驗,將管理、設備、技術、人員、信息有效整合,建立基于數(shù)據(jù)采集的設備管控系統(tǒng),實現(xiàn)設備故障早期預警和人機系統(tǒng)精細化、智能化管理,全面提高工作效率和工作質量。
- 上一篇:TPM液壓油的選用及防污染控制方法
- 下一篇:TPM關于設備潤滑管理的探討